Reports From the Field: Boiler Survey
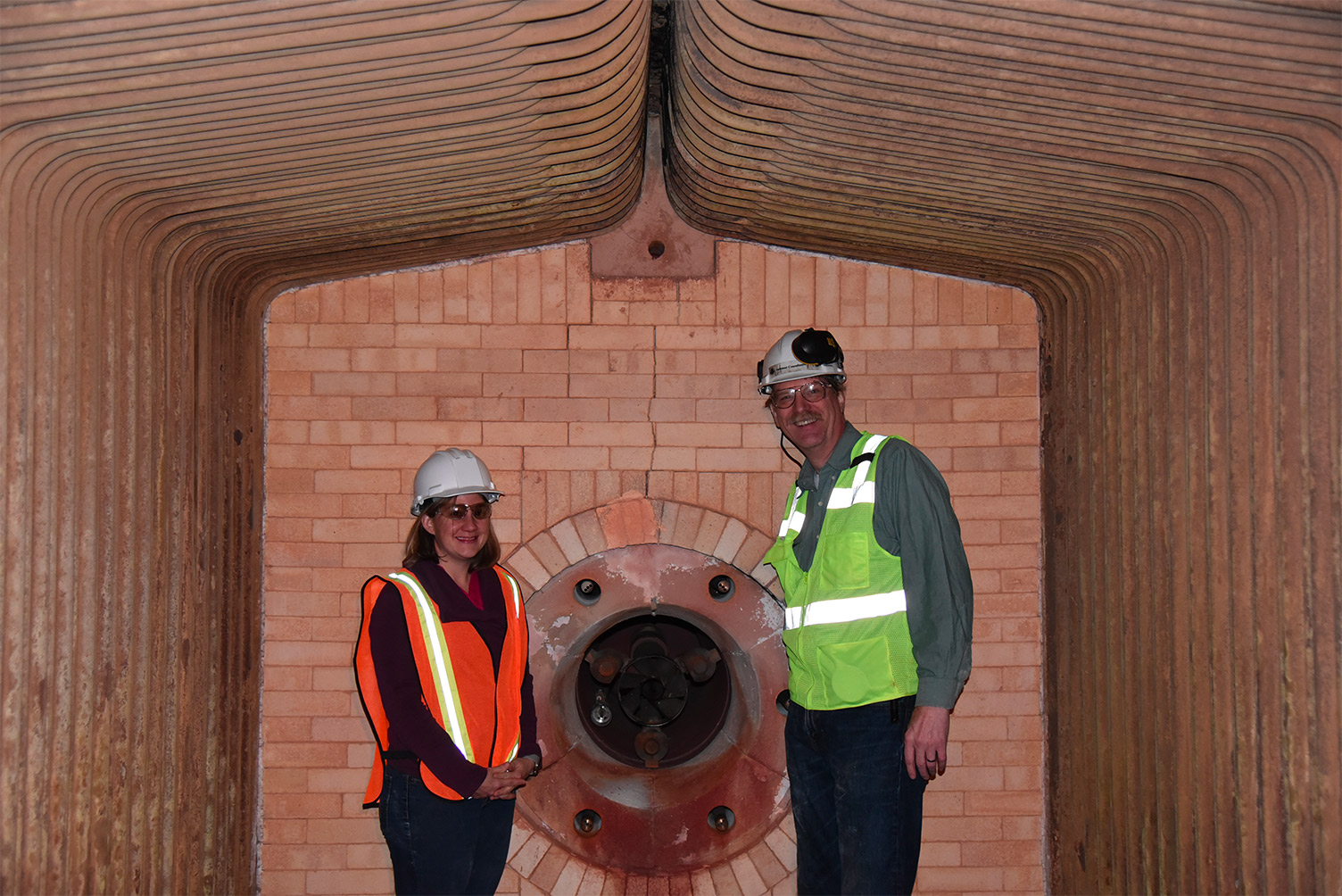
Recently on a job, I had the opportunity to experience and gain some first-hand knowledge about large industrial water tube boilers. I went on a field survey with our “Boiler Guru”, Pete, and gained my first experience being inside a boiler. This boiler was built and installed in 1961 and is dual fuel, meaning that it can be operated both on gas and oil. One of the first things I got to do was crawl inside the boiler to learn about the different components of the boiler. He pointed out that the tubes inside the boiler had some water damage and even picked up the floor bricks to show me the patterns in which an A-Style Boiler tubes were constructed inside of the boiler itself. I learned that there are three things a boiler inspector and operator looks for to ensure that the boiler is operating under normal conditions. The first and most important is the water level, which is displayed by a large water gage that is on the very front of the boiler. The second most important is the water chemistry. This can be tested when cold water is used to cool the boiler water in a sample cooler. Water contains impurities that if not removed before entering the boiler can cause the boiler to malfunction which could result in an explosion. The third most important thing when it comes to boilers is ensuring that the fire within the furnace is burning correctly. Another thing that was stressed to me was the importance of having a clean boiler especially in the area of the burners and combustion air intakes.
I was involved with inspecting the performance and burning testing of four boilers. Each boiler was tested burning both natural gas and oil. Two of the four boilers operated normally with no major issues, but two of the boilers had issues firing on oil and have low air. Low air causes the pilot to trip and shuts down the burner. One boiler would not even fire the pilot when running on oil.
From our on-site inspection, I also had the opportunity learn more about how boilers are manufactured or repaired. The outer casing is bent from large 10 gauge steel sheets. The folded up edges are seal welded to make the boiler gas tight. To withstand the pressure in the furnace, there are ribs that are stitch welded to the casing. These ribs are important, because when tubes inside the boiler need to be replaced they can be easily removed, but inside this particular boiler we found the tubes to be in great condition.
Comments