The Art of Fire Protection Design
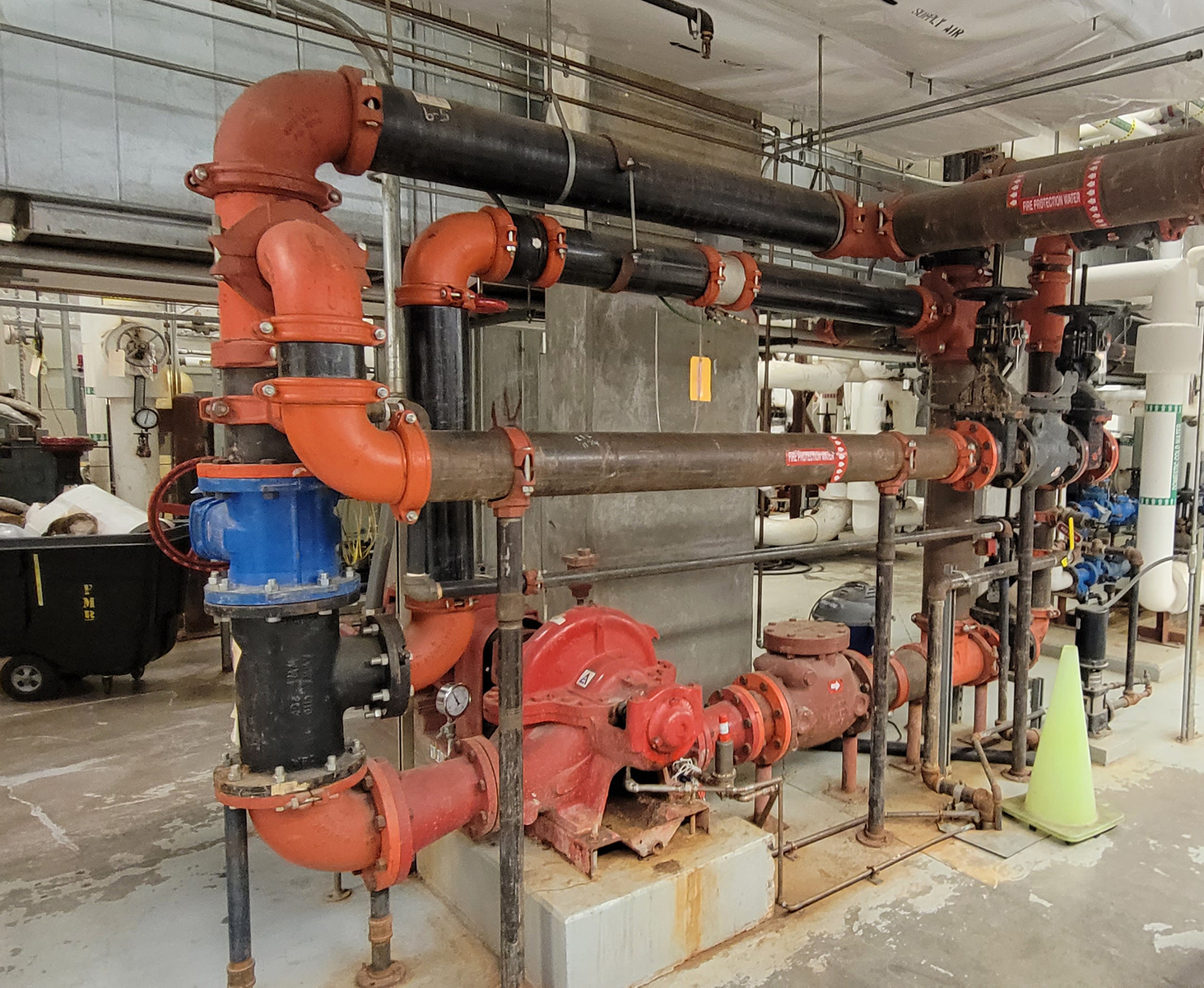
I began my career in the fire protection field as a consultant engineer. My main duties consisted of surveying facilities for fire hazards and recommended improvements, including the repair, replacement or provision of new fire protection systems. Now, as a licensed fire protection engineer, I am designing the systems that are to be improved or installed.
While a code compliant (i.e. NFPA) design is a significantly important step in the process of properly protecting facilities, it is hardly the only step. All steps, including correctly identifying the hazards, developing an appropriate design, reviewing the installation, and proper maintenance of the systems, are all equally important. An error or exclusion during one step along this path can render the fire protection systems ineffective. The easiest way to ensure all steps are properly completed, is to not think of each step as its own silo, but rather a collaboration throughout the process.
In my current position, I focus on creating code compliant fire suppression and alarm designs. However, it isn’t enough to just meet code requirements, because there are times when meeting code does not mean that the system is constructible. Other times, the system can be built, but it will cost tens of thousands of dollars a year to properly test and maintain.
There are many examples of this, but the most common examples that I have come across are the design and installation of complicated fire suppression systems and equipment that exceed what is needed for the given hazard or space that is being protected.
One example of this would be installing special protection systems, such as preaction sprinkler systems, when they are not required. Preaction sprinkler systems have a specific purpose and are certainly a valuable system to have in an engineer’s toolbelt; however, they should only be used when completely necessary, as everything about a preaction system is more complicated than a typical wet sprinkler system. Preaction systems are usually most beneficial areas with freezing temperatures, in crucial electronic equipment rooms (sometimes as backup to another suppression system), and in rooms with high-valuable or rare items with potential impact of sprinkler heads or piping. However, even in these cases, the design should consider the most basic sprinkler system possible.
Take an MRI room in a hospital, for instance. These rooms historically have been provided with preaction system for the fear of having water located above equipment that is usually valued at over a million dollars. While it is true that preaction systems do not keep water in the pipes above the room, the additional installation and maintenance requirements involved with preaction systems often outweigh the benefits. These systems regularly include a cabinet which contains the valves and trim for the riser and that cabinet takes up a large amount of valuable floor space. The pipes are typically either galvanized piping or are inerted with nitrogen to prevent scaling. With either design, the cost of installation increases dramatically.
Once installed, the upkeep of these systems is complicated as it involves trip testing, internal investigations of valves and piping, and releasing device testing. Because of the complexity of the systems, this maintenance is often completed incorrectly or overlooked altogether, which leads to the room with the expensive equipment not being protected at all in the event of a fire.
Another example would be the use of diesel fire pumps (right image) over electric fire pumps (as shown in top image). There are perks to diesel fire pumps, and they are usually used when the primary electric power to the facility is not stable or reliable. However, it is usually more desirable, from a maintenance perspective, to install a dedicated emergency generator for the fire pump and life safety systems over installing a diesel fire pump. Diesel fire pumps require weekly churn testing for 30 minutes, compared to electric fire pumps, which need churn testing for only 10 minutes on a monthly frequency. Similarly, the diesel fire pump requires maintenance similar to a car engine (battery testing, oil changes, filter changes, etc.) that an electric fire pump does not. Other factors, including operating noise, installation and equipment costs, and floor space requirements, also favor electric fire pumps.
As mentioned before, cost isn’t the only thing that can prevent a design from being implemented. A good design also considers the ease of installation. A key factor in preparing for a smooth installation is how disciplines coordinate their work during the design process. Fire sprinkler pipes are typically tucked up above suspended ceilings. In that space, there is also lighting, conduit, plumbing, HVAC, structural members, etc. It isn’t as easy as designing a straight run of pipe through the middle of a corridor. In renovations, it is common to have to route pipe around existing construction and utility features. While it looks like the pipes fit in your design software, whether CAD or Revit, it is always good to take a step back and consider if there is adequate access to the space for installation purposes. Can two or three people get a 10-foot (or longer) piece of pipe above the ceiling, between the conduit run and hot water pipe and over top of the existing duct work? Typically, not the easiest thing to do. A good design will take this into account and attempt to reroute the pipe in another location.
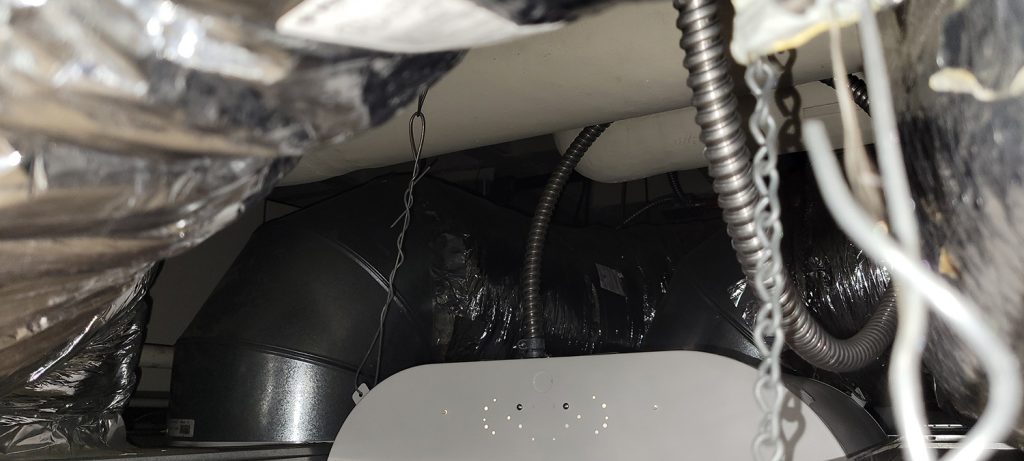
In summary, designing a fire suppression system to meet minimum code requirements is not good enough in many circumstances. Installation ease, cost, maintenance, testing requirements, and individual facility needs all factor into a high-quality design. Experience with all aspects in the field of fire protection, from design conception all the way through maintenance of the systems, allows a fire protection engineer or designer to design the best possible system for the specific facility or hazard. My suggestion to engineers is to get in the field as much as possible and survey, observe testing and installation, and continue to learn.
Comments